I always underestimated cyanotypes and the emotional power they contain. Simple things are like that. One color, limited tones, and simple formulas help me connect with feelings and ideas like no other process. This winter, I’m digging into the process, pulling out negatives from my archives that deserve a new viewing.
Read MoreAlternative Processes
Teaching a Tintype Workshop /
Teaching Tintypes.
I was in a darkroom teaching a tintype/wet plate collodion workshop at the New England School of Photography. I’ve been teaching at the NESOP for about twenty years and it never gets old.
Teaching tintype is the epitome of “slow photography” and that is important. Students left with under ten finished plates each and that was a successful weekend. In a fun twist, when wet plate collodion and was the “latest and greatest” technology of the day (1860’s), it was the fastest process being used.
Why teach (or take) this workshop?
It’s good to slow down.
Learning the history of a medium builds a deeper understanding of its present iteration.
The sound of running water in a darkroom is peaceful.
It’s fun.
I often think of the classes I teach as “play-dates” for adults. While they can inspire larger bodies of work, most of the time, it’s just a fun weekend of trying something new.
The most successful students are the ones who just have fun splashing around, asking questions, and making stuff for a few days.
I always leave these weekends a little tired but energized. The curiosity of the students is contagious and delightful. While I know more about the mechanics of the process I’m teaching (I hope), I’m still learning how to teach it effectively. That journey never really ends. For that, I’m grateful.
Read MorePlatinum es mi Papi! /
Making Platinum Prints
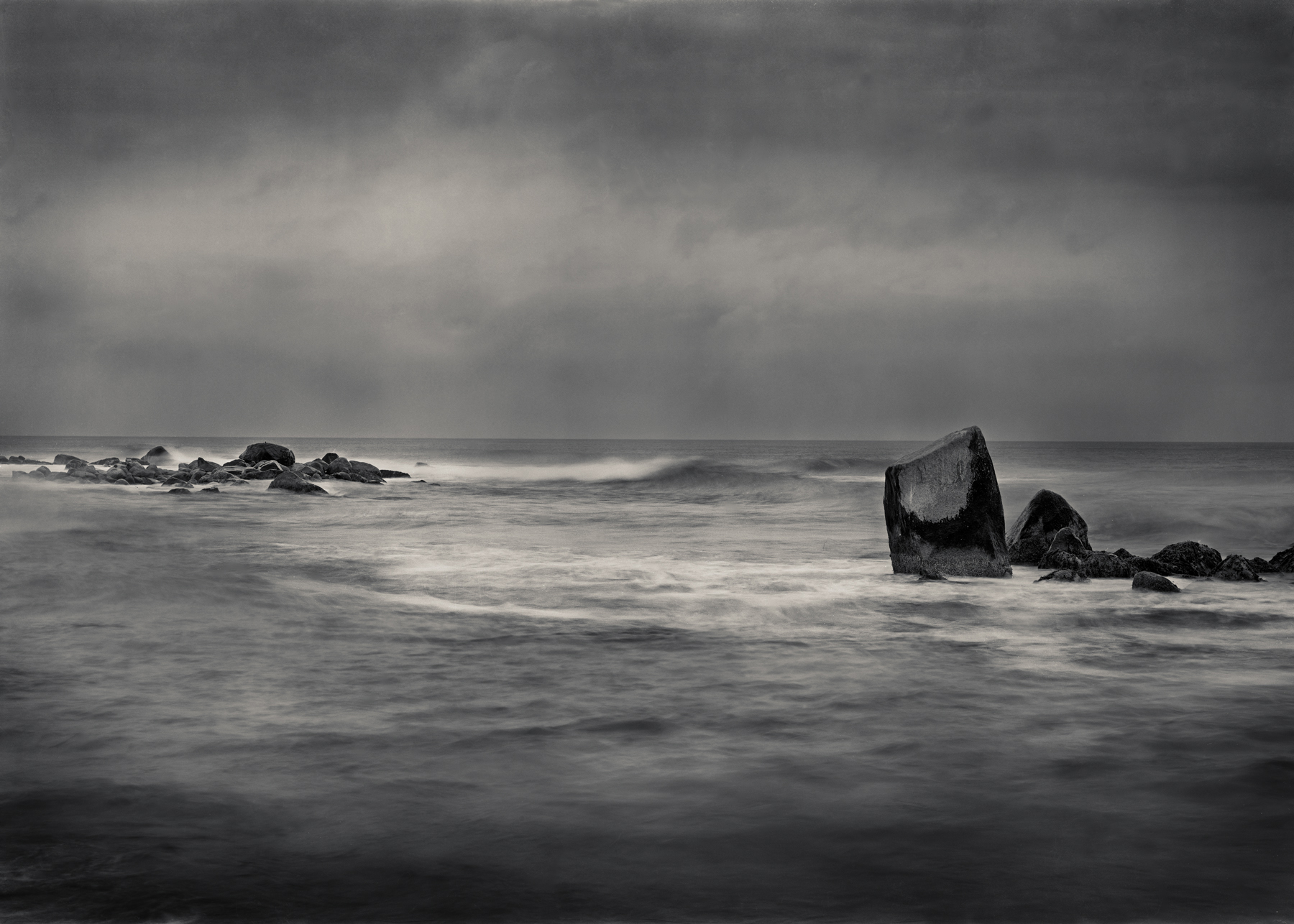
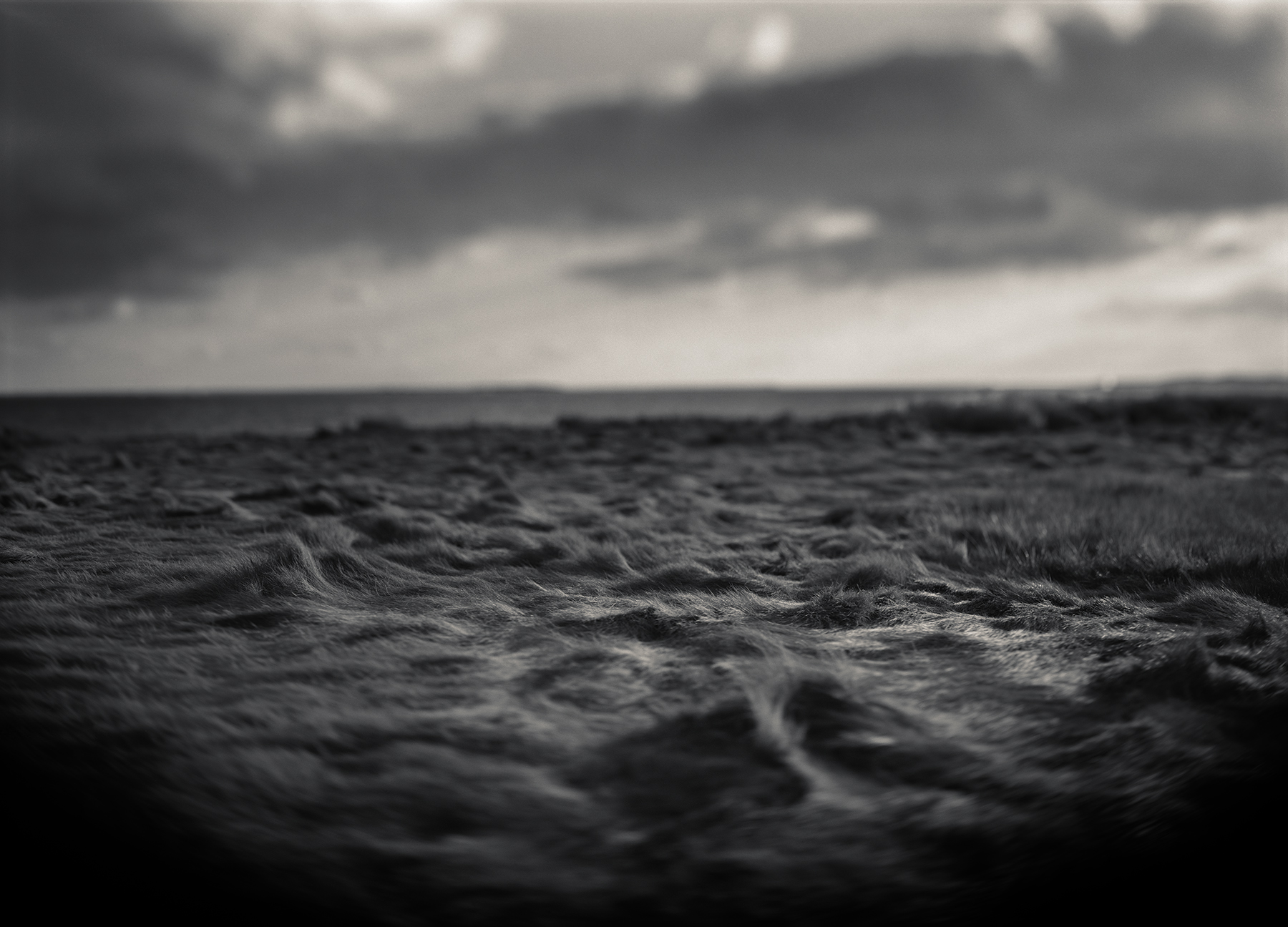
Platinum images are known for their long tonal scale and contrast range. Early prints would be considered too flat (no blacks) by today's standards but, "back in the day" they were considered the "bee's-knees". Platinum prints will never have blacks (Dmax) to rival silver paper but the benefits outweigh the drawbacks.
I realize that the above paragraph, if taken out of context is totally racist.
Printing from an in camera negative.
Since platinum printing is a contact printing process, the size of the image is determined by the size of the negative. Before digital negatives, a photographer had two choices:
- Print images from original large format negatives
- Create enlarged negatives.
- Before digital negatives came about (a very welcome thing), enlarged negatives were an art form in and of themselves. It was a two-step process involving printing the original negative onto a positive sheet of film and then printing that image onto a larger sheet of film to the desired print size. As with any multi step process, a little detail was lost with every step.
- With pictorialism, this wasn't such a bad thing.
Today, only an insufferable hipster geek would make enlarged negatives in the darkroom. The first thing he/she would need to get is a time machine since the materials went away in the early part of the 20th century. So, digital negative or in-camera negatives it is. Be happy.
In Camera Negatives
In camera negatives should have a good contrast range. Your highlights should be fairly dense and you shadows should be pretty open. Usually, I just take an average meter reading and overdevelop my film one or two stops. Let's not make high mass out of this
A lot has been said about developers and I have switched between Pyro PMK and XTOL. My main film is Ilford FP4.
Digital Negatives
Today, thankfully, inkjet printers have replaced the enlarged negative issue. Now a photographer can make a negative as large as the inkjet printer can handle. I think this has become a little ridiculous with wall sized platinum prints. After a while, what's the point besides demonstrating how much money you can burn.
Methods
There are several methods for calibrating your inkjet printer to your platinum print. All of them claim to be better than the next. At the end of the day, find a method that gives you consistent results and preserves your sanity. There is a learning curve to all of them. Here are the two most popular methods
- Mark Nelson's Precision Digital Negative
- I use this system and have enjoyed good results. He has since updated it but I have stuck with an earlier version.
- Quadtone Rip
- Some of my favorite platinum printers use this process. What I know about it could fit in a thimble.
General Printing
A platinum print is usually made with three separate solutions.
- Ferric Oxalate (sensitizer)
- Platinum Solution
- Palladium Solution
You can adjust the contrast in a variety of ways: Hydrogen Peroxide, Dichromate in the sensitizer, developer temperature, or more than one of these methods. Currently, I'm using the Na2 method of platinum printing where the contrast agent is in the platinum solution.
Developer
There are two different types of developer commonly used in platinum/palladium printing:
- Potassium Oxalate
- Ammonium Citrate
Potassium Oxalate is used if you want a warmer print since it works well at higher temperatures. Ammonium Citrate is good for a nice, neutral print at room temperature.
A few things to keep in mind about either developer: NEVER THROW THEM OUT!! The developers never go bad and actually, with regular replenishment and filtering, you can have the same working developer for years. You will always lose a little developer in the printing process and just add some fresh developer at the end of your session.
As I mentioned, Potassium Oxalate is pretty versatile and can be used at room temperature or upwards of 110-120 degrees. The increase in temperature will lower the contrast and increase the brown tones.
Clearing Agents
The purpose of using a clearing agent is to get the iron out of the print and leave the platinum/palladium. Think of it as fixer. There are a variety of clearing agents and formulas. I have used a dilute solution of Hydrochloric Acid but stopped after burning a hole through some plumbing pipes and having the skin on my fingertips kind of vanish.
Here is my current solution which seems to be the industry standard now.
2 Tablespoons EDTA
1 Tablespoon Sodium Sulfite
1 liter water
You make three trays of this clearing agent and as the first tray gets exhausted. You'll know as the color turns to rust brown. Simply dump that tray, move the second one down and refill the empty to place at the end of the line. Prints should stay in each clearing bath a minimum of ten minutes. You don't want to see any yellowish stain in your highlights since that is iron oxide (rust) and will stain your image and corrode it as well.
Rinse in running water for about 20 minutes. I hang my prints to dry to avoid contamination with screens.
Final Thoughts
As you may have already noticed, there are many ways to successfully make platinum/palladium prints. Believe me when I tell you it is the source of many mildly interesting conversation in hotel lobbies with other printers. The nuances of printing are many and we haven't even gotten into the papers you can use for this process. Currently, I'm using COT 320 with good results. That might change if the paper changes. The paper is going to change.
Platinum Printers of Note (Starting with the one's who answer my phone calls).
- Keith Taylor
- Sal Lopes
- Kerik Kouklis
- Lois Conner
- Beth Moon
- George Tice
- J. Keith Schreiber
- Dick Arentz
- Tom Millea
- Irving Penn
- Scott B. Davis
- Peter Henry Emerson
- Anne Brigman
- Laura Gilpin
- David Michael Kennedy
- Tillman Crane
Resources (where to buy what you need)
Not a very long list. Both of these businesses are the best and very helpful. Support them.
Exhibitions and Interesting Links
- All That Glitters Is Not Gold --- Phoenix Art Museum
- Truth And Beauty, Pictorialist Photography --- Museum Of Fine Arts, Boston
- The Collection at The MET
- Understanding Photographic Processes
- Photoeye Gallery Search By Process
Cyanotypes, My Blue Mistress. /
Cyanotypes Shouldn't Be Ignored
The cyanotype is one of the oldest photo processes. It is also the most humble and under appreciated. How can a process that only has two ingredients, develops in water, and lasts forever be so maligned?
I’ll tell you why. It is because the cyanotype was never intended for that fancy, uptown photo stuff. The cyanotype was “invented” so a guy could copy is lab notes on the cheap.
From its humble start, great things have been made with this process. It is worth starting our journey here for a variety of reasons.
Cyanotypes are inexpensive to make.
Why spend all your hard earned cash on chemicals when you don’t have to? For less than fifty dollars you can make a gallon of sensitizer. Consider the amount of sensitizer it takes to make one print (about 2ml) you’re looking at a lot of soup to play with.
Cyanotypes are simple but offer a great deal of variation.
You can adjust the intensity and contrast of the tones through adjusting the Ph of the water. Vinegar or citric acid is the simplest solution (in every sense of the word).
Cyanotype Recipe
What you need
- Ferric Ammonium Citrate
- Potassium Ferricyanide
- distilled water
- brown bottles. with eye droppers
Solution A
- 25 grams Ferric Ammonium Citrate (green crystals)
- 100 ml distilled water
Solution B
- 15 Grams Potassium Ferricyanide
- 100ml distilled water
Mix equal parts of each solution into a small cup (plastic or glass is ideal). Swirl around the solution to make sure they are mixed. Pour onto your paper and with a glass rod or damp brush move the solution around to cover the desired area.
At this point it is important to let the paper absorb the light sensitive solution. This means letting the solution sit in a dimly lit space. While the cyanotype process is only sensitive to ultra-violet light, exposure is cumulative so it makes sense to reduce the amount of light that hits the paper whenever possible. Just walk away.
While it is not necessary, I have found the addition of a solution called “tween” to be helpful in providing an even absorption. What tween does is break down the surface tension of the solution so it is absorbed evenly.
Once the coated paper has an even matte surface (careful not to touch because it is still wet) take a blow drier and put it on the warm setting. Dry the paper completely.
Exposure
The fun part about cyanotypes is the simplicity of printing. This is an inspection process which means you check your print as you go. This is done by using a contact printing frame with a split back. This allows you to open up the back, peel the paper away from the negative and check how the exposure is going.
When the print looks like you want it to look, it needs to be exposed for a longer time. The ideal finished exposure should have all the shadows blocked up and the highlights about 2 times darker than desired.
The reason for this is during the development process, the exposed material on the paper surface washes away. I layman's terms, the print lightens up.
Full development has occurred when the yellow-green stain has been washed out of the highlights or unexposed parts of your print.
Toning Cyanotypes.
Most materials you need to tone a cyanotype can be found in the baking or laundry aisle of your grocery store. These are just a few of the items you can use to alter the color and contrast of your cyanotypes. There are two phases of toning: bleaching and toning. The bleach phase comes first.
- Borax (For bleaching)
- Sodium Carbonate (Bleaching)
- Tea (Red Rose or Lipton) for toning
- Tannic Acid (toning)
- Wine Tannin (toning)
- Citric Acid (Changes color to teal)
This is not a comprehensive list. Here are some links that discuss cyanotype toning in greater detail.
- General toning information
- Multi-Colored Cyanotypes
- Comparison of Toning techniques
- Tim Rudman's Tea Toning